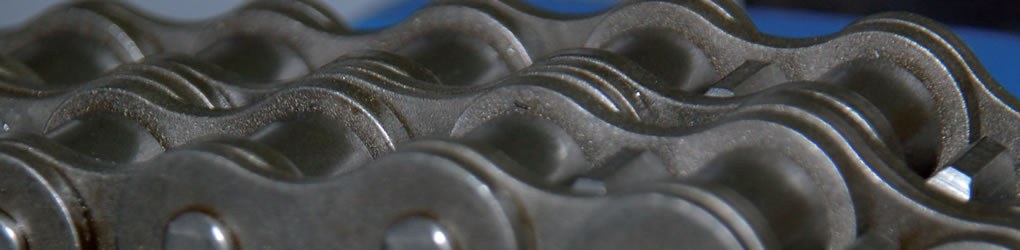
Stack turnover & panel turning devices
Turning large and heavy stacks, boards or packages
It is used for the most different reasons. Production processes make it necessary to turn the material. Therefore the material is collected and turned as a stack before it is fed back into production. This is often the easier option than turning each individual part separately. For large dimensions or weights, the turning of individual parts is preferable.Another reason is to replace the carrier plate or pallet because it is damaged or to change to a cheaper shipping pallet. It may also be necessary to change from external pallets to your own load carriers, or to align the material or product during turning.
Turning by hand is usually not possible due to the amount of work involved, the dimensions or the weight. Therefore, an automatic solution must be found that is suitable for the product and its dimensions and weight. Over the years, SYSTRAPLAN has developed a wide variety of tailor-made solutions. In the usual solid SYSTRAPLAN design we can offer you the right turner according to your requirements.
This video will be loaded from Google YouTube.
Their privacy policy applies.
Their privacy policy applies.
A technical design which makes the difference
Solid and custom-made design
The stack turnover consists of the base frame with rotary drive, the turnover frame as well as the platforms and the side stop. The underframe is made of standardized profiles in welded and bolted steel construction. The rotary drive is installed in the underframe. The turning rings are driven by an electric gear motor acting directly on a continuous drive shaft with 2 VULKOLLAN®-banded drive wheels mounted on it.
The turning rings are tracked in the base frame by flanged wheels. Integrated in the tedder frame is a platform that can be raised and lowered by electric motor and a permanently installed platform. The platforms are also made of standardized profiles in welded steel construction.
The lifting drive of the platform is carried out by an electric gear motor and sliding scarifier acting on a chain drive, which drives 4 ball screws. After the turning process is completed, the stack is lowered to the discharge level by the movable platform and the stop for stack removal is moved to the side.Stack turnover as a stand-alone solution
Integrated turnover device in the production process
The throughput turner would be integrated into the production process. The pile or board enters on a roller conveyor, is turned and exits automatically. The necessary conveyors for automatic infeed and outfeed are mounted on the lifting platforms of the turner and the working height is adjusted accordingly. Even with low infeed and outfeed heights, the turner can be integrated into existing systems, if necessary with the help of a pit.
Side stop to hold the material
Integrated pallet clamp for pallet change
The clamp is integrated into the platform of the turnover unit to hold and lift an upside down empty pallet. The empty pallet is thus placed on top of the stack and is located under the stack after the turning process. The pallet then lying on top is clamped and lifted before the stack is discharged.
Examples of use:
- Pallets with full-size or half-size decorative papers, also known as foil pallets or decorative pallets. This is particularly common in the lamination of chipboard in the wood-based materials industry.
- Stack turnover device in the furniture industry for turning entire stacks of furniture parts between processing steps.
- In the prefabricated house industry, house walls are turned during the production process.
These are only a few examples, the applications of the turners are complex and can be found in the most diverse branches of industry.
References
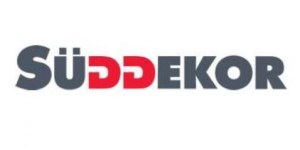
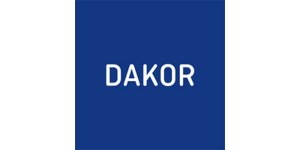
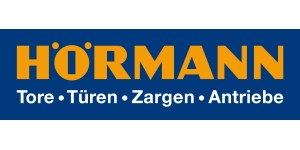
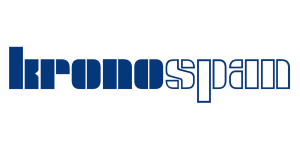
Stack turnover & panel turning devices
We are developing solutions today for your future needs
Let us know your individual requirements.
We will work out a concept tailored to your needs
We will work out a concept tailored to your needs