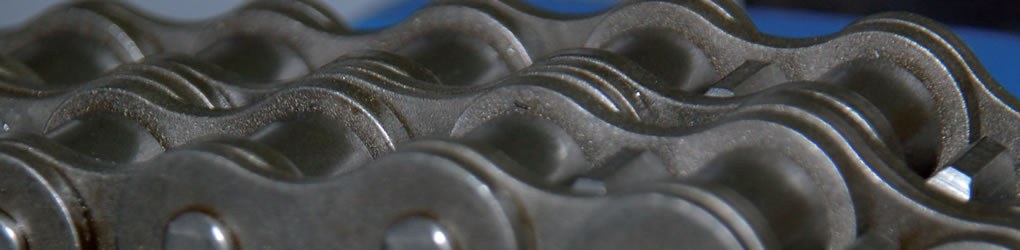
ROBOTIC TREAD BOOKING
Loading treads automatically into leaf trucks
Automatic tread booking systems from SYSTRAPLAN are well known in the tyre industry, but now there is an alternative solution based on a KUKA robot.Faster extrusion speeds and the need for greater accuracy encouraged tyre manufacturers to replace manual loading with automatic tread booking systems. More and more booker loading systems have been installed to overcome the problems associated with manual loading.
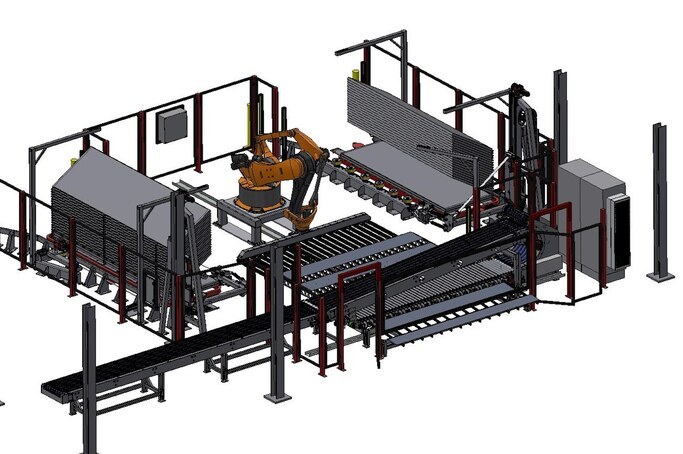
Advantages of an automatic tread booking system
Increased output due to higher extrusion speeds
Faster extrusion speeds and requirements for higher accuracy encouraged the tire manufacturer to replace the manual loading of the treads by automatic tread booking systems.
More and more tread booking systems were installed in order to overcome the disadvantages associated with manual tread loading, but above all to be able to realize a higher extrusion speed and thus increase the output of the entire production line.Reduction in manpower
Tread deformation is a good example. Improper handling can cause transversal and longitudinal deformations. Especially dimensions and weight of truck treads make it hard for operators to handle the treads in a proper and appropriate manner.
Automatic tread booking avoids the disadvantages associated with the manual tread handling.
Reduced machine downtime
Over many years, SYSTRAPLAN has developed and perfected its tread booking systems. Many details have been improved to ensure a better and faster maintenance or possibly repair in order to reduce machine downtimes and to raise the reliability of the automatic tread booking systems.
The PowerTwist belts are used for transportation. These belts are non-welded and can be replaced easily and fast without using tools.Improved product quality
Tyre quality depends on correct transport and storing of treads.
It does not matter what leaf truck type is used or whether the treads need to be flipped or not, what counts is the accurate and uniform and gentle depositing of the green treads on the trays of the leaf trucks to guarantee a constant high quality.
The advantage of the belt tray lies in the fact that the treads always keep on lying on the belts with a tight spacing and due to their own weight; and the surface can be finely structured or freshly cemented as it is not touched.
Technical design
The key components
Main components of an automatic robotic tread booking systems:
- Cross transfer, vacuum flipping or boomerang
- Cross transfer conveyor system for batch formation
- Robot with suction frame of belt tray for loading the leaf trucks
- 2 leaf truck loading positions for an uninterruppted loading process
- Automatic leaf fold-down in combination with down holding elements
- Electrical control (Allen Bradley, Siemens)
Suction frame or belt tray
Handling the charge for loading
Two different systems are available for handling the batch of treads for loading:
A conventional surface suction frame which picks up the treads from the top, for a belt tray which picks up the batch from below, as it has been done for years in automatic tread booking systems.
The advantage of the belt tray lies in the fact that the treads always keep on lying on the belts with a tight spacing and due to their own weight; and the surface can be finely structured or freshly cemented as it is not touched.
Which system is used depends on the customer's requirements.
Loading positions
2 leaf truck loading positions for an uninterruppted loading process
Two loading positions for leaf trucks ensure uninterrupted production. While one leaf truck is being loaded on one side, the full leaf truck is replaced by an empty truck on the other side without the process being stopped.
Leaf folding
Separate leaf folding ensures cycle time
A leaf folding device at the end of each leaf truck loading position automatically closes the next leaf while the robot picks up the next batch. With this simultaneous mode of operation, a high cycle time can be achieved.
Benefits of Robotic Tread Booking
Cost-effective
Robots can work for long periods without breaks and require less supervision compared to human workers. This translates to lower labour costs in the long run.
Space-saving
Robotic tread booking systems can be designed to be compact and efficient, minimizing the footprint needed in your facility compared to our traditional automatic tread booking systems.Customized solutions
Robots open up enormous potential for the development of customised solutions. The following points illustrate the wide range of possibilities. Robots are flexible and can be customised to individual requirements. They can be programmed to perform different tasks and adapt to different environments and products. This enables the development of customised solutions that are perfectly tailored to the customer's needs.
Quicker and easier to implement
Robotic systems often require less upfront setup and training compared to complex automatic booking systems. This can get your tread booking operation up and running better with less interruptions.
Minimal maintenance
Robots are generally built for reliability and require less frequent maintenance compared to some complex machinery. This translates to less downtime and disruption to your production schedule.
Sustainable and environmentally friendly
Robots can potentially reduce energy consumption compared to some traditional systems. Additionally, they can minimize the risk of human error that might lead to material waste.
Tread Booking Systems
We are developing solutions today for your future needs
Let us know your individual requirements.
We will work out a concept tailored to your needs.
We will work out a concept tailored to your needs.
Optionen
Automatic leaf truck transport
Insert manually, position automatically
An automatic leaf truck transport system automatically positions the leaf truck for loading. The trolleys simply have to be pushed between the first pressure rollers of the automatic leaf truck transport system. The transport system automatically positions the trolley once the operator has left the safety area.
Manual booking
For a manuel loading of the leaf trucks and for removing rejects, a manuel handling station may be integrated upstream or downstream of the automatic booking system.
In case the manuel handling station is to be integrated downstream of the automatic loading point, the treads are conveyed straight through. In principle, there a several options for the design of a manuel handling station.
Material flow options
One of the main challenges for the design of the booking system is to bring the treads in the correct orientation.
In order to feed the treads in the right direction into the automatic booking system the flow of material coming from the extrusion line has to be individually planned.
Depending on the requested cycle output, various combined options may be used.
In order to feed the treads in the right direction into the automatic booking system the flow of material coming from the extrusion line has to be individually planned.
Depending on the requested cycle output, various combined options may be used.
Angular transfer station with vacuum flipping
The vacuum-turner flips the bottom side of the incoming treads. While doing so, the arms of the turner equipped with vacuum suction cups dive through the spaces of the feeding roller conveyor in order to suck in the pre-positioned treads from below. The treads are then turned at an angle of 90° and positioned on a transversal belt conveyor. A performance of a cycle output of up to 2, 4 seconds can be achieved.
Angular transfer station with lateral transfer station
When operating with high cycle times the lateral transfer station gets as well as the vacuum turner into action, but the tread is not turned. The arms of the lateral transfer station dive through the feeding roller conveyor and take up the tread from below. During this process the tread is kept in constant balance. The tread is transferred in the same orientation to the transversal belt conveyor at an angle of 90°.
Angular transfer station
When manufacturing with cycle times greater than 3 (three) seconds, an angular transfer station may be used instead of the lateral transfer station. The roller distance and the distance of the transferring belt conveyor are narrow enough to guarantee a safe transport and support without deforming or stretching the treads.
INTRALOX DARB™ Übergabe
An INTRALOX DARB™ conveyor can transfer treads 90 degrees without stopping. This increases the throughput compared to conventional angular transfers or enables a lower line speed.
Reliable and low-maintenance operation is ensured by only a few wear parts and a simpler control system.
This video will be loaded from Google YouTube.
Their privacy policy applies.
Boomerang