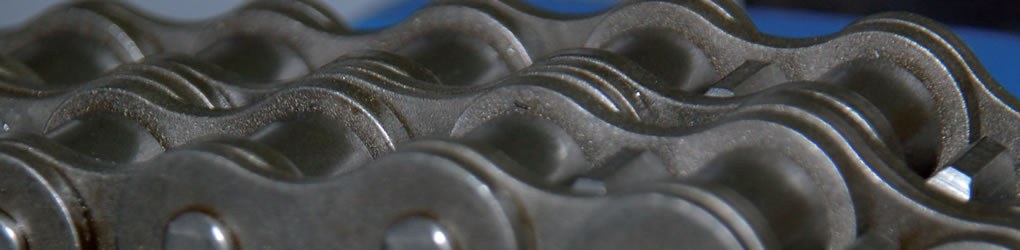
TREAD BOOKING SYSTEMS
Quality improvements with the use of automated tread booking systems
Automatic tread booking devices from SYSTRAPLAN are well known and used in the tire industry for quality assurance of treads and tires as well as for rationalization. SYSTRAPLAN, specialist for warehouse technique when it comes to flat materials, has a long history in building auto booking and handling systems for the tire industry.The experience we have gained over the years in building this system in large quantities has been put into practice. Since its establishment in 1974, SYSTRAPLAN has delivered more than 100 automatic and semi-automatic handling systems for treads, green and finished tires. This machine type has been further developed on basis of experience gained with a large number of machines.
This video will be loaded from Google YouTube.
Their privacy policy applies.
Their privacy policy applies.
Advantages of an automatic tread booking system
Increased output due to higher extrusion speeds
Faster extrusion speeds and requirements for higher accuracy encouraged the tire manufacturer to replace the manual loading of the treads by automatic tread booking systems.
More and more tread booking systems were installed in order to overcome the disadvantages associated with manual tread loading, but above all to be able to realize a higher extrusion speed and thus increase the output of the entire production line.Reduction in manpower
Tread deformation is a good example. Improper handling can cause transversal and longitudinal deformations. Especially dimensions and weight of truck treads make it hard for operators to handle the treads in a proper and appropriate manner.
Automatic tread booking avoids the disadvantages associated with the manual tread handling.
Reduced machine downtime
Over many years, SYSTRAPLAN has developed and perfected its tread booking systems. Many details have been improved to ensure a better and faster maintenance or possibly repair in order to reduce machine downtimes and to raise the reliability of the automatic tread booking systems.
The PowerTwist belts are used for transportation. These belts are non-welded and can be replaced easily and fast without using tools.Improved product quality
Tyre quality depends on correct transport and storing of treads.
It does not matter what leaf truck type is used or whether the treads need to be flipped or not, what counts is the accurate and uniform and gentle depositing of the green treads on the trays of the leaf trucks to guarantee a constant high quality.
The advantage of the belt tray lies in the fact that the treads always keep on lying on the belts with a tight spacing and due to their own weight; and the surface can be finely structured or freshly cemented as it is not touched.
Technical design
The key components
Automatic tread booking systems that handle up to 30 treads per minute are composed of the following major components:
- Feeding roller conveyor with variable speed drive
- Manual booking station for rejected treads
- Vacuum flipping or lateral transfer station
- Cross transfer conveyor system for batch formation and storage
- Lifting platform with belt tray for loading the leafs for the leaf trucks
- Automatic leaf fold-down in combination with down holding elements
- Automatic leaf truck conveyor system
- Electrical control (Allen Bradley, Siemens)
Tread loading with lifting platform and belt tray
Accumulation for auto booking
The treads are transferred from the transfer belt conveyor to the downstream belt conveyor where the treads are collected to a batch with a precise determined spacing between the treads.
The number of treads is pre-selected by the operator and depends on the tread width and the depth of leaf truck leafes available.
Following attached are further conveyors / cross transfers for buffering complete tread batches.
Auto booking of leaf trucks
After buffering the complete batch is taken from the belt tray. Provided that an open leaf truck is available, the belt tray with the tread charge moves into the open leaf truck.
After reaching the end position in the leaf truck, the belt tray is retracting while the belts move forward at exactly the same speed. In this way, the tread batch is held in a fixed position in relation to the leaf truck side and is thus deposited in an exact position on the side of the leaf truck.
The modern charging head with belt tray consists of the following major components:
- Belt tray with variable moving stroke and driven belts
- Automatic leaf fold down-device with hold-down elements
- Belt tray lifting with spool system for quick level adaption
- Servo drives in combination with customers standard PLC
Automatic leaf truck - side folding device
During the loading process, the automatic folding device ensures that the upper leaf of the trolley does not interfere. After the loading process, the underside of the next flap of the leaf truck is sucked in by vacuum suction cups and pulls the leaf to an angle of approx. 30° from the horizontal.
In this position, pneumatically activated hold-down devices coming from above take over. The vacuum cups are released and swivel out of the area of the side of the leaf truck. The hold-down devices fold the side into the completely horizontal position for the rest of the way.
After the belt tray has completely moved out of the leaf truck again, the next tread charge waiting on the belt conveyor of the loading head is taken over and the next loading cycle can begin. Instead of lifting the belt tray to next level of the leaf truck, the complete leaf truck is lowered so that the next leaf can be loaded.
Faster cycle times thanks to folding device
The synchronized movements of the downholder pressing down the leaves of the leaf truck as well as as the folding device that opens the leaf with the suckers for the downholders result in a reduced cycle time.
With this new folding device the leaf folding process is one smooth motion ensuring a faster folding.Automatic leaf truck transportation system
Different systems for the leaf truck transportation
The automatic leaf truck transport can be adapted according to the different trolley types.
Our standard solution is a leaf truck driven by single-sided, vertically rubberized rollers. Here the book trolley is pressed against driven rollers by spring-loaded or pneumatic pressure rollers.
Many different solutions for leaf truck transport have already been implemented in order to meet the requirements of different types of leaf trucks.
Continuous production thanks to automatic leaf truck change
After the complete leaf truck has been loaded, it is automatically moved out from the loading station and another leaf truck, which is in waiting position, is brought into loading position. This enables a continuous work flow without interruption. The operator then pushes a new, empty leaf truck into the waiting position.
In the meantime, the arriving treads were collected and buffered on the belt conveyors. At the same time the loading head lowers to the lowest loading position of the next empty side of the leaf truck.
Options
Leaf truck transport with lateral exit
If the leaf trucks are pulled by means of a tow truck, the automatic feeding of the leaf truck can be equipped with a separate lateral exit for the tow truck allowing the truck to be driven out after uncoupling before the automatic loading station.
The length of the automatic leaf truck transport system is thus extended accordingly. Safety is ensured by an automatic sliding gate.Leaf trucks
In addition to our automatic tread booking systems, we are also happy to offer you the matching leaf trolleys. We design the leaf trucks individually for your requirements and product dimensions.
A sturdy, yet lightweight construction ensures durability and the simplest possible handling. The leaf trucks offered by us are ideally suited for our automatic leaf truck transport on the leaf truck systems.Aligning of treads
In some cases it makes sense to align the treads upstream of the angular transfer station in longitudinal direction before they are crosswise conveyed. With little space the aligned treads can be collected to a charge. By this means, a small packing density can be obtained.
The alignment is accomplished by means of an INTRALOX-conveyor with cross rolls and a synchronously travelling upright belt conveyor. This belt conveyor can be adjusted to the tread width by using the axle.
Manual booking
For a manuel loading of the leaf trucks and for removing rejects, a manuel handling station may be integrated upstream or downstream of the automatic booking system.
In case the manuel handling station is to be integrated downstream of the automatic loading point, the treads are conveyed straight through. In principle, there a several options for the design of a manuel handling station.
Manual booking - roller conveyor
The simplest option would be a basic roller conveyor – on request with lateral positioned deposit tables – integrated into the material flow. In this case, the incoming treads are directly taken off the roller conveyor.
Manual booking - angular transfer station
It should be provided that treads or rejects can be buffered by means of an angular transfer station with transverse belt conveyor. Depending on the length of the cross conveying line, a corresponding number of treads can be buffered.
Manual booking - angular transfer station with vacuum flipper
In order to flip the treads, the angular transfer station of the manuel handling station may be equipped with a vacuum-turner.Work - Off handling for treads
More and more companies are realising the necessity for an automated process of treads that have been rejected for rework. SYSTRAPLAN has developed various solutions that are able to fully automate this handling process. The solutions are always adapted to the needs of the customer.
Outward transfer through manual removal
The solutions for a manual removal of treads as described before can also be used for collecting rejected treads. Whilst the system is operating in automatic mode, a manual removal station already in place can also serve as a collecting and removal station for rejects. Instead of placing the rejected treads in the leaf truck, they are manually stacked on a pallet.
However, in order to ensure the outward transfer of the rejected treads automatically whilst the flawless treads are manually taken off, additional devices should be provided.
Solutions for the handling of rejects
The simplest option to realize this procedure is to convey the rejected treads by means of a somewhat extended roller conveyor onwards and straight through a slot, which is integrated in the protective fence, where these then fall uncontrolled on a pallet.
Other solutions allow the formation of small stacks of rejected treads and thus the collection of more treads. Several solutions have been realized in the course of time. The cycle output needed and the available space on site are significant approaches to find the appropriate solution.
“Ejecting star“– angular transfer with stack forming
A simple rake ejection star or angular belt conveyor integrated in a roller conveyor laterally ejects the treads, either directly on a palette or on an INTRALOX®-conveyor for forming small stacks. Thus the piles are more or less formed in a controlled way, depending on the treads and speed of the system.
Leaf truck - leaf folding with a robot
Instead of two standard leaf folding devices, is a robot installed in the centre of the lifting frame of the belt tray equipped with a suction tool for sucking in the opened sides of the leaf truck. The robot is simultaneously lifted by the lifting platform of the belt tray.
The robot sucks in the leaf from below and opens it wide enough to enable the pneumatically activated down-holder to hold the leaf from above. The robot’s suction cups are released and swivel out of the range of leaf truck’s side. The down holders are then folding the leaf further down till a complete horizontal position is gained. The robot-leaf-folding-device achieves the required faster cycle times just like the standard devices.
This video will be loaded from Google YouTube.
Their privacy policy applies.
Harmonious motion, reduced downtimes
With this robot-leaf-folding-device the closing of the leaf truck side is a harmonic and smooth motion with the additional benefit of less wear and low maintenance requirements for the system. The robot used is resilient and requires little maintenance, which results in reduced downtime of the entire system.
Various opening angles possible
The robot can handle leaf trucks with different opening angles. These leaf trucks can be successively processed, there is no conversion needed. New types of leaf trucks can be easily integrated into the process through a Teach-In function. The leafes of the leaf truck are loosened and opened in a safe and gentle way.
The benefits at a glance:
- Use of a low-maintenance standard industrial robot,
- Less wear, less maintenance, reduced downtimes,
- Harmonic and smooth motion sequence,
- Gentle handling of leaf truck leafs,
- Reduced noise pollution when folding leafs,
- Handling of leaf trucks with different opening angles possible,
- New opening angles easy to program by Teach-In,
Tread Booking Systems
We are developing solutions today for your future needs
Let us know your individual requirements.
We will work out a concept tailored to your needs.
We will work out a concept tailored to your needs.
Material flow options
One of the main challenges for the design of the booking system is to bring the treads in the correct orientation.
In order to feed the treads in the right direction into the automatic booking system the flow of material coming from the extrusion line has to be individually planned.
Depending on the requested cycle output, various combined options may be used.
In order to feed the treads in the right direction into the automatic booking system the flow of material coming from the extrusion line has to be individually planned.
Depending on the requested cycle output, various combined options may be used.
This video will be loaded from Google YouTube.
Their privacy policy applies.
Their privacy policy applies.
Angular transfer station with vacuum flipping
The vacuum-turner flips the bottom side of the incoming treads. While doing so, the arms of the turner equipped with vacuum suction cups dive through the spaces of the feeding roller conveyor in order to suck in the pre-positioned treads from below. The treads are then turned at an angle of 90° and positioned on a transversal belt conveyor. A performance of a cycle output of up to 2, 4 seconds can be achieved.
Angular transfer station with lateral transfer station
When operating with high cycle times the lateral transfer station gets as well as the vacuum turner into action, but the tread is not turned. The arms of the lateral transfer station dive through the feeding roller conveyor and take up the tread from below. During this process the tread is kept in constant balance. The tread is transferred in the same orientation to the transversal belt conveyor at an angle of 90°.
Batch turning device with rake
The batch turning device is integrated into the angular transfer conveying line in automatic booking system direction. This system collects first a complete batch on the transversal belt conveyor for one side of the booking system.
Two rakes with separate lifting and lowering functions are installed to a rotatable column. One rake lifts the batch and turns it by 180° whilst simultaneously a previously taken up batch is placed down. This solution with two synchronically working rakes guarantees a high cycle output.Batch Turning device with transversal belt conveyor with lfting and lowering function
This system is also first collecting a complete batch on the transversal belt conveyor for one side of the automatic booking system. One transversal belt conveyor with lifting and lowering function is integrated into the cross conveying line in automatic booking system direction.
The batch collected is taken over, lifted by the transversal conveyor and placed down again. This solution allows a rotation of the charge as well as a conveying of the charge through without turning.
Angular transfer station
When manufacturing with cycle times greater than 3 (three) seconds, an angular transfer station may be used instead of the lateral transfer station. The roller distance and the distance of the transferring belt conveyor are narrow enough to guarantee a safe transport and support without deforming or stretching the treads.
INTRALOX DARB™ Übergabe
An INTRALOX DARB™ conveyor can transfer treads 90 degrees without stopping. This increases the throughput compared to conventional angular transfers or enables a lower line speed.
Reliable and low-maintenance operation is ensured by only a few wear parts and a simpler control system.
This video will be loaded from Google YouTube.
Their privacy policy applies.
Boomerang