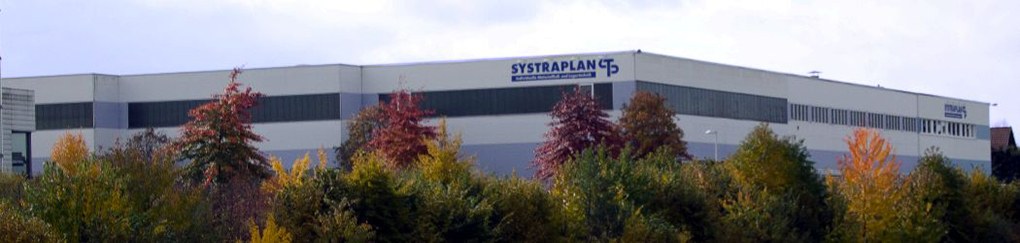
Our History
For 50 years a trusted partner in automated storage and material handling
For half a century, SYSTRAPLAN has been developing state-of-the-art material flow and storage concepts for the wood and furniture industry, the building materials, plastics and metal processing industries as well as for the granite and tyre industry. With the right material in the right place at the right time, the company ensures optimised production processes.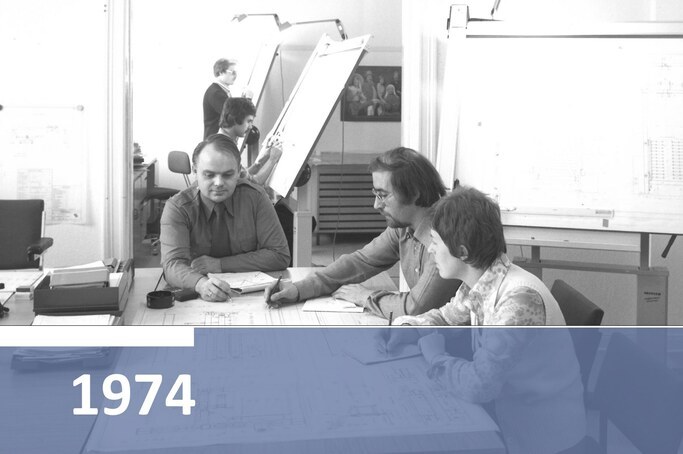
Panel handling as a core competence
The original idea when Dr Jostmeier founded the company in 1974 was to offer panel handling for panel cut-to-size saws for the wood-based materials and furniture industry. This was initially done in co-operation with the Schwabedissen company, also based in Herford, which sold the corresponding saws at the time.
The founder's inventiveness quickly developed a momentum of its own, which resulted in numerous solutions that no longer necessarily had anything to do with sawing.
The original premises on Diebrocker Straße in Herford quickly became too small, so the company moved to a new location on Einsteinstraße in the Heidsiek industrial estate. Over the years, this was expanded to 4,500 square meters of production space.
Despite all the changes, the specialization in handling panel-shaped materials of all kinds has remained the same even after 50 years.
Customized material handling and storage technology
SYSTRAPLAN's customized and tailor-made systems are still a synonym, especially in the wood and panel industry. With the storage and retrieval machines developed by SYSTRAPLAN, both packages and individual panels are moved and picked gently. In addition to transporting entire packages and individual panels, picking takes place directly on the storage and retrieval machine. This principle has also been adapted for other flat materials and branches of industry.
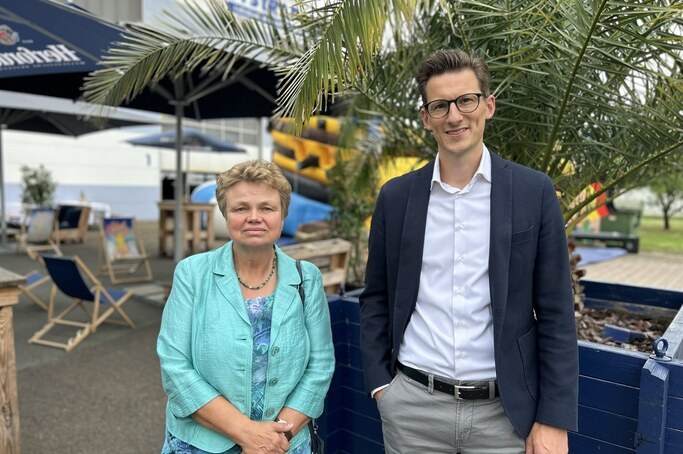
SYSTRAPLAN made a name for itself in the tyre industry with its so-called automatic automatic tread bookings systems. Shortly after the company was founded, initial contacts were made with the tyre industry. They were looking for a solution for the automatic handling of the still warm and soft rubber treads. With decades of experience, SYSTRAPLAN has consistently developed the tread bookng system further. Over 100 of these systems are now in use worldwide to ensure the current quality standard of tyres.
Family business in the second generation
SYSTRAPLAN is still an owner-managed family business in the second generation. Silke Jostmeier, the daughter of the company founder, joined her father's company in 1993 after studying business administration. After her father retired from the operative business in 2002, she took over the management of the company together with Werner Krutemeier. Today, she shares the management with Florian Krutemeier, who has been with the company since 2018 and took over the technical management in 2023.
Oure Milestones
1974 Founded by Dr Jostmeier
The company was founded on Diebrocker Straße in Herford. The original idea when Dr Jostmeier founded the company was to offer panel handling solutions for panel cut-to-size saws for the wood-based materials and furniture industry. This was initially done in co-operation with the Schwabedissen company, also based in Herford, which sold the corresponding saws at the time.1977 First tread booking system for the tyre industry
Shortly after the company was founded, initial contacts were made with the tyre industry. They were looking for a solution for the automatic handling of the still warm and soft rubber treads. This was to be the foundation stone for numerous other systems for the tyre industry.1978 Move to the company premises on Einsteinstrasse
The original premises on Diebrocker Straße in Herford quickly became too small, so the company moved to a new location on today's Einsteinstraße in the Heidsiek industrial estate.1990 Inauguration of the extension building on Einsteinstrasse
Existing space was utilised to gradually expand the production area over the years. Today, production takes place on an area of 4,500 square metres. The company has also invested in new production facilities to meet increasing demand.
1992 High-bay warehouse for automated picking of wood-based panels for the furniture industry
The ever-increasing variety of decorative panel materials required automation of the panel storage system with direct access to the individual panel materials. For this purpose, SYSTRAPLAN developed a storage and retrieval unit with a suction frame for separating the panels directly in the shelf compartment and then feeding them directly to a panel saw.1996 Rack serve carrier with combined lifting platform
Thanks to the intelligent combination of lifting platform (access to a single shelf) and stacking platform (transport of entire stacks), these rack serve carriers offer optimum features for effective and space-saving storage.1999 First compact sorting memory for sorting and buffering
The increasing number of variants with simultaneous order-related batch size 1 production makes it necessary to pay greater attention to the optimisation of material flows in production in order to be able to use processing machines and materials even more efficiently. Today, it is impossible to imagine industrial production without such storage systems.
2002 Dr Jostmeier hands over to his daughter
After 28 years with the company, Dr Jostmeier retired from day-to-day business in 2002. He handed over the management of the company to his daughter Silke Jostmeier. Mrs Jostmeier has been responsible for the commercial side of the company since 1993. Since her father's retirement, she has been supported by Werner Krutemeier as the other technical managing director.2003 Europe's largest high-bay warehouse for the timber trade
SYSTRAPLAN received an order from Carl Götz GmbH in Neu-Ulm, one of the leading timber retailers in Germany, for the construction of a storage and distribution centre for wood-based materials. Two 24 metre high SRMs each serve two aisles. In contrast to conventional SRMs, this system works with two lifting platforms that are controlled independently of each other.2006 Area storage with integrated stack transport
SYSTRAPLAN has developed a new area storage system that is able to handle both individual panels and complete stacks with the same conveyor. Stacks of panels are stored completely in one cycle. The system is adaptable in terms of formats and stack heights and can therefore be used flexibly.
2009 Presentation of the VOLKSLAGER concept at LIGNA
This new and more cost-effective concept is particularly interesting for companies that have previously invested in an area storage system for cost reasons. With the simple but efficient storage and retrieval machine presented by SYSTRAPLAN, higher performance is guaranteed by faster access to the different panel variants in the rack compared to an area storage system.2016 New monorail rack serve carrier
Storage system with 24 m high stacker cranes have already been realised in the past. New development of a new generation of high stacker cranes in which the design of the side masts was significantly optimised with the help of a synthesis of stability and weight optimisation.2022 Change in the technical management
On 31 December 2022, Mr Werner Krutemeier ended his active role as Managing Director and handed over technical management to his son Florian Krutemeier, who has been with the company since 2018.2023 Robot tread booking system for the tyre industry
A tread booking system based on a KUKA robot was presented for the first time at IRMRA 2023 in India. This cost-effective technology impresses with advantages such as space savings, quick and easy implementation and low maintenance requirements.