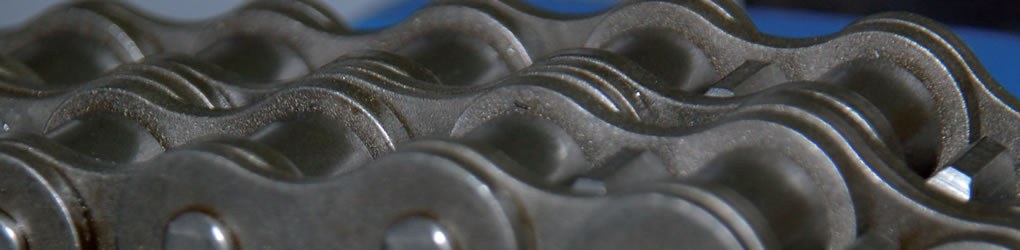
BUFFERING, SORTING and ORDER PICKING
Improving efficiency by optimization of the material flow
Increasing number of versions in combination with 1-piece production at the same time require an optimization of the material flow in the furniture industry to allow an even more efficient use of the processing machines and materials.
The use of a compact sorting warehouse for the optimization of the material flow can play an important role.
With the help of a compact sorting warehouse, the work piece will be temporarily stored between each individual processing step and is then made available just-in-time in a new optimised order for the following processing step. This does not only allows optimizing the production process when manufacturing furniture components, but also opens up entirely new possibilities to a more rational production.
The use of a compact sorting warehouse for the optimization of the material flow can play an important role.
With the help of a compact sorting warehouse, the work piece will be temporarily stored between each individual processing step and is then made available just-in-time in a new optimised order for the following processing step. This does not only allows optimizing the production process when manufacturing furniture components, but also opens up entirely new possibilities to a more rational production.
This video will be loaded from Google YouTube.
Their privacy policy applies.
Their privacy policy applies.
Applications
Fields of application
All areas of application result from the various production stages of the particular product. This applies not only for instance in the field of furniture production:
Panel cutting – edging – drilling – CNC machining – surface – assembly – packaging.
But also for different branchesAims of a sorting warehouse system:
- Optimization of active processing times
- Optimization of resetting times
- Smoothing of production capacity
- A more even production, lot-size-1 provided
- Allowing several orders for the next shipping date as well as further orders of the same machine operation, so
- called “can-pieces” that are provided by the buffer at a later point in time
- Same manufacturing time for A-, B- and C-products
- Just-in-time feeding of processing machines directly from the sorting warehouse
- Best possible utilisation of the resources
- Minimisation of waste
The sorting warehouse operates respectively optimizes various tasks individually or in combination.
A production control system performs the stock administration, the management of the entire processes as well as the optimization based on the criteria individually defined.
Storage and automatic batch forming
Work pieces that are fed into the sorting warehouse are identified with bar-coded labels. Depending on the part length, several work pieces are collect by the system and moved to the appropriate section of the compact sorting warehouse. These are then layer-wise picked up by the operator unit, which is in standing position, by means of telescopes.
Ideally, all parts can be stored within one level. In the worst case, each part has to be stored in a different level – depending on the sort key.
For the following processing step, i. e. a sizing and edge processing machine, the batch is automatically formed in accordance to the pre-set priorities, such as thickness, colour, edge type, edge colour or distemper.Higher capacity utilization of the processing machines
When forming batches, the system tries to find the maximum occupancy of the sizing and edge process machine and as few as possible resetting times. The objective is, to achieve a continuous occupancy of the processing machines.
Work pieces that have been completed within one cycle, are discharged and replaced by a following work piece, and thus, no engine idling arise.
Sorting criteria
Typical sorting criteria in the manufacturing of furniture parts:
- Preview of edges for the edge banding machine
- Saw optimisation with residue registration and administration
- Feeding with pre-sorting and allocation procedure, i. e. for edging = thickness, edge type, edge decors, adhesive and order number or i.e. saw
- Board thickness
- Edge colours
- Adhesive colours
- Data of drilling diagram
- Selection drilling machine/CNC: Which kind of process takes longer on which machine?
- Selection/ allocation to machine in general
Individual definition of sort criteria
All sort criteria will be customer-specific determined together with the customer and accordingly considered on the software. It is also possible to declare different processing objectives.
Several cycles for the same machine, in each case with further sorting in the warehouse are also possible. The return of the work pieces back to the sorting warehouse theoretically can be repeated as often as required.Consideration of additional parameter
Before the production control system moves any part, the software takes thickness, colour and design of the later edges as well as the actual fill level into consideration. This also applies for the preview of all subsequent processes that follow the compact sorting warehouse.
Only after having taken account of all these parameter, the sawing optimisation asks for the next board that is to cut. In order to gain better options for the best appropriate cutting pattern, the systems allows to cut work pieces of subsequent jobs, which are then buffered in the compact sorting warehouse. The residues are recorded and administered.
Content of the manufacturing guidance system
1. Sorting buffer incl. transport routes for feeding and discharging of parts
- Stock administration of buffer stock
- Control and monitoring of all transport routes
- Control of operator units
- Visualisation of the complete system
- Implementation of assortment logic
- Current stock overview of sorting warehouse and sorting progress.
- Possibilities for a manual intervention, i. e. special retrievals of parts or modification of the order of a lot.
- Optimisation of transports in order to store or retrieve as many as possible parts per cycle.
2. Planning module
- Import of all necessary data from the customer.
- Storage of the data in a data base.
- Central planning module for the cutting.
- Display of all outstanding jobs for the saw.
- Grouping methods for the display and selection of the parts to be manufactured.
- Production of batches in relation to the sorting capacity of the system.
- Display of the filling level of the sorting unit.
- Data transfer to the optimisation core.
- Taking over of the optimisation results.
- Printing of staging lists for the cutting.
Resorting for subsequent process step
Work pieces that are returned from the sizing and edge processing machine to the warehouse will be, taking following processing steps, such as drilling and/or CNC machining into account, resorted and stored.
After a new batch has been formed this will be removed from stock and fed to the following processing step, again taking the specific requirements and criteria of the work piece and the technical possibilities of the machine into account.Ideal flow right from the start
If certain parts are required for assemblies or packaging, the system fully automatically brings the parts in correct order - despatch date and the maximum allowed capacity of the following processing step taken into account.
In order to maintain optimum machine performance and to work as efficiently as possible with the overall system, right from the start this system takes all processing steps of each work piece into consideration.
Sorting and buffering systems
We are developing solutions today for your future needs
Let us know your individual requirements.
We will work out a concept tailored to your needs
We will work out a concept tailored to your needs
Technical design
Direct access to individual parts
The systems are mechanically built like a stationary storage and retrieval system that is completed by a cantilever rack on the right and left side. By placing the single work pieces directly on the cantilevers, the system allows a tight design of each single level corresponding to the board thicknesses. This warehouse system allows different level sizes for different thicknesses of panels, but the actual advantage of this system is the direct access to each section of the level and thus a speedy access to each single part.
Classification into sections
The compact sorting warehouse is lengthwise splitted in sections of equal length. The length of each section depends on the average piece length. The telescopic system of the manipulator unit is divided in identical sections that can be operated individually or combined.Multi-deep storage
For an optimum use of the arms depth, the lifting platform has a shifting device placed between the telescopes. Smaller parts are positioned during the stroke in such way to make it possible to place other parts before these parts in the same level. The high packing density of the system is achieved by combining the sections. The parts are multiple-deep stored in a large number of sections applying for each level to both sides of the manipulator unit.
Example of compact sorting system
Based on the usual working piece dimensions used in the furniture industry – that is approx. 1.000 x 500 mm -, one sorting warehouse has a capacity of max. 1.320 parts with a cantilever depth of approx. 1.300 mm and 6 sections with the appropriate length and approx. 55 levels on the left and right side of the operator unit, roughly corresponding to a hall height of ca. 6 m. When planning an efficient sorting system individual requirements are essential.
Further sorting warehouses can be installed in a row without any problems to be in line with the capacity or screening needed by linked machines or buffer capacity.High mechanical cycle performance
The mechanical cycle output of a sorting warehouse comes to approx. 3 cycles per minute. This means, at best, with assumed 6 separate sections on the operator unit that 3 by 6 parts per minute could be transported.
The quantities that are to be stored within a warehouse and the required cycle times must be taken into consideration on the basis of part sizes, installation dimensions and weights in designing the system.
Based on the data gained, it may be decided how many warehouses – this might be one, two or more - are needed.
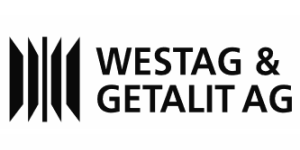
Sorting System Westag
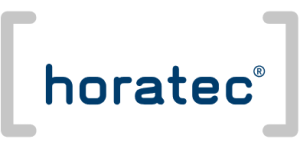
Sorting System Horatec