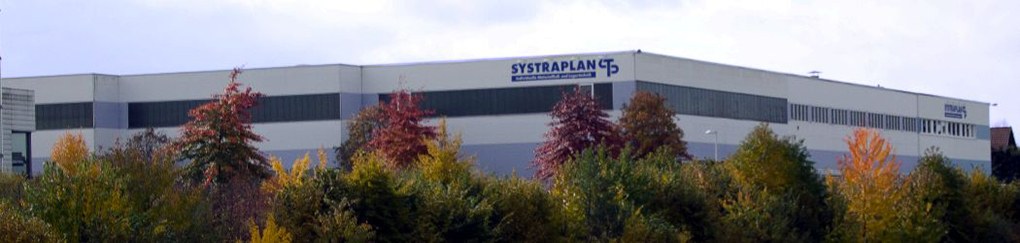
SERVICE & MAINTENANCE
Prompt service is servicing customers
With this foundation, SYSTRAPLAN offers optimum customer support across the entire product life cycle, from the design phase and development of the ideal solution, to the technical project handling and through to the commissioning by our experts. But even after that we are by your side with a comprehensive range of services.We support you with maintenance of your machine in order to avoid unnecessary and expensive repairs. A regular maintenance through our well trained technicians means prevention and ensures a long service life of your system.
This requires flexibility and quick response. SYSTRAPLAN offers competent and reliable services for both preventive machine maintenance and short-term machine repairs.
Good to know
Identification of the system for inquries
For inquiries and a simple identification it is helpful if you are able to tell us the number of the machine or serial number – consisting of a four-digit number – as well as the position number. You will find this on your system on the machine tag.
Inspection- or maintenance contract
We will be happy to provide you with an offer for an inspection- or maintenance contract. Your machine shall be inspected through an experienced skilled technician at regular intervals. Then repairs or replacements of wear and spare parts needed can, subsequently, be planned and carried out without any time pressure. Downtimes and the involved production loss are thus avoided.
VPN-interface
The controls of our systems are equipped, as a rule, with VPN-interfaces. We support our clients with the fault diagnosis in a quick and competent way, provided our clients ensure the access to the required internet connection. In this way malfunctions of the system can often be located and solved online.“Pro-Active" Maintenance
Downtime costs time and therefore money, therefore regular maintenance, as well as "pro-active" maintenance is essential to increase the efficiency of the equipment. With regular inspections, the need for repair is identified in advance. Before the system fails due to defective components, these are replaced. The service can be well prepared and scheduled so that production downtimes are avoided as far as possible. Spare parts are procured "just in time" in advance. The principle "action instead of reaction" increases efficiency.
Your advantages with preventive maintenance from SYSTRAPLAN
High quality of workmanship with optimum cost-benefit ratio
Our qualified skilled workers, technicians and engineers ensure a high-quality, efficient and sustainable maintenance process. We make this process transparent for you so that you can keep an eye on the costs at all times.Individual solutions for your needs
We do not deliver a solution "off the shelf". A cooperation with SYSTRAPLAN guarantees you a solution that is individually tailored to the requirements of your company and continuously optimised.The process in transparent steps
Maintenance is carried out in steps, traceable and after prior consultation with the customer:- Request of the customer
- Offer and order by the customer
- Determination of the date of implementation in coordination
- Order of spare parts and consumables by arrangement
- Personnel planning for the maintenance date
- Maintenance implementation
- Documentation of the maintenance
Autonomous processing
SYSTRAPLAN handles scheduled and unscheduled measures on its own responsibility. This means that we take care of all preparations and post-processing ourselves. This includes the procurement and provision of spare and wear parts. In addition, we take care of the necessary testing and measuring equipment and, if necessary, call in the necessary specialists.We are on site for you
The cooperation with SYSTRAPLAN in preventive maintenance pays off: We reduce downtimes, optimize the availability of your machinery and thus increase your operational reliability. For this purpose we employ experts from the fields of electrical, mechanical and mechatronic engineering.
Our team is there for you:
Rafael Tajuelo
Installation / Plant management
+49(0) 52 21 / 76 77 - 51

+49(0) 52 21 / 76 77 - 51

Karl Müller
Maintenance
+49(0) 52 21 / 76 77 - 58

+49(0) 52 21 / 76 77 - 58

Andreas Schmitz
Spare parts
+49(0) 52 21 / 76 77 - 57

+49(0) 52 21 / 76 77 - 57

Please write us
Right here: