12.September 2017
Perfectly sorted and automatically ready to be dispatched
Publication from the HOLZENTRALBLATT from 1.9.2017
The shipping of ready-made worktops at Westag & Getalit is organized by SYSTRAPLAN’s sorting system.
ck. The increasing diversity of parts in line with order-related batch size 1 production makes it necessary to optimize the material flow in the furniture and supplier industry. This especially applies for the last process station - the dispatch. Only recently, Westag & Getalit had a sorting system in Wadersloh installed. This was manufactured by SYSTRAPLAN for optimum processes and maximum efficiency.
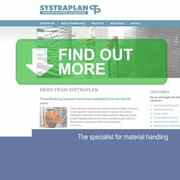
Kitchen worktops are just as individual like the kitchen itself. In 1974, the Wadersloh facility was constructed specifically for the production of worktops, as an expansion of the headquarters based in Rheda-Wiedenbrück. Here the batch size 1 production has been standard for many years. Today, the Wadersloh facility provides surfaces/elements and supplies for European kitchen manufacturers, DIY stores and the timber trade under the brand name “Getalit”. All customers have unique requirements in order sizes and worktop panel dimensions. “Standard becomes less and less”, says Josef Michels, plant manager at Westag & Getalit in Wadersloh. The new SYSTRAPLAN sorting system was installed and operational in June 2017.
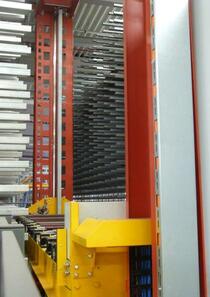
In the year 2000, SYSTRAPLAN, located in Herford, built a first of type sorting system for worktops. Contrary to expectations and, a few years later, this system became increasingly important in the assembly lines. This was due to an increase in the diversity of parts and high production output demand, thus demonstrating interlinked production systems cannot do without sorting solutions.
„As early as in the planning stage of such a sorting system, important basics must be taken into account”, explains Lutz Abel, graduate engineer and Sales Manager at SYSTRAPLAN, whom from the beginning has been responsible for the Westag & Getalit project.
All dimensions will be adapted to customer specific requirements.
„The decision about the best concept solution is based on parameters such as size, diversity of parts, performance including the peak load requirement.” Thus, SYSTRAPLAN compact sorting systems are used for average-sized storage capacities but also when high performance is required at the same time to store and remove parts. They possess a high cycle output because there is no axle in longitudinal direction.
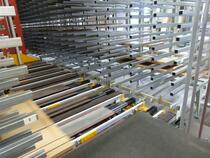
For Westag & Getalit, however, other requirements were applicable and a “standard” sorting system was the perfect choice. “If a high storage capacity is required and the partial performance is low to medium as it is the case here, our sorting system is the right choice”, says Abel. With this solution a storage and retrieval machine moves within a rack aisle, equipped with a specific load suspension and operating as a sorter. The high storage capacity is achieved by the length of the cantilever rack, resulting in a high packing density because parts are stored in rows that are multiple deep.
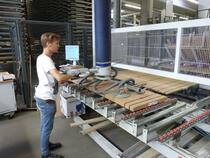
The cantilever rack is individually customized to the dimensions of the parts. The system at Westag & Getalit stores panels ranging from 650 to 5,360 mm in length and 350 to 1,400 mm in width. Worktops with a maximum depth of 65 cm can then be stored in a row as described before. In this case the panels’ thickness may not exceed 14 to 39 mm, and 59 mm in the designated storage level. “But there are also different distances from level to level possible for the various panel thicknesses within the sorting system.”, explains Abel, “This depends on the customers’ requirements”.
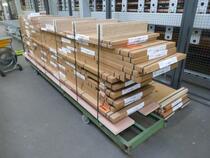
For Plant Manager Josef Michels, the new sorting system from SYSTRAPLAN means the beginning of a new era at the end of the process chain. “Not long ago there were many trolleys for racks here, where we are standing right now, next to each other. And they were manually loaded with the worktops freshly packed”, he says. “This was not only very time-consuming, it also involved great efforts to pool the orders for the same customer.” The result was that there were too many line items, in the worst case, allocated on several trolleys. Nowadays, we are able to automatically combine such orders, i. e. for a DIY store”. The same obviously applies for customers from the kitchen industry with major orders. These orders alsoo are pooled to be processed faster and for swift loading. Such pooling becomes visibly apparent on a bundled stack, and the comparison with a trolley for racks – there is still a number of them existing – it exemplifies the progress being made.
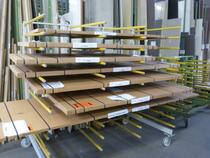
The order pooling takes place manually due to the safe stacking of single boards. The single parts coming from the sorting system are all well packed in individually made folding cartons. But this is not sufficient for a safe transport. The folding cartons are manually or via vacuum cups – depending on weight and size – taken over, then placed on squared timber and finally strapped. The software of the sorting system controls the relocation sequence in such a way that the longest parts of a stack are placed first to form a secure package. Another factor for forming the package are specially manufactured parts with cut-outs or notches. These elements are individually positioned on a support according to pre-specified criteria or in a pre-specified position within the package to avoid breaking in two and to ensure optimum transport protection. The operator at the retrieval position of the sorting system has to make sure that any differences in height are compensated. This is necessary, because, otherwise, there will be no safe stacking (cargo securing) possible with other batches on the vehicle.
Impressive performance of the software made by 3TEC
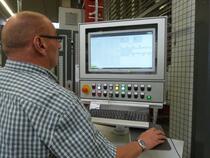
This following describes the central task of the sorting system: The release of the panels from stock in a determined order for the subsequent dispatch. When it comes to system controls, SYSTRAPLAN relies on the software made by the specialists at 3TEC, located in Vlotho. It is very impressive what this software can actually do – this is shown by the example of the sequence when removing panels or worktops from stock. Not less impressive is the visualization of the processes in the sorting system. All parts are shown on the monitor along with the levels where these parts have been placed. Even the panel’s thickness is visible. It is also possible to follow the movements within the warehouse in real time.
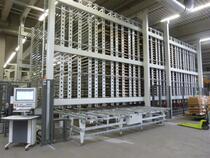
Thereby the operator can choose between a cross section view of the sorting system and a top view showing single levels. “I can virtually “touch” each single part with the mouse or monitor”, says Ralf Damhuis, responsible for operational planning. “The system provides all data right away, such as dimensions or the corresponding customer.” The system knows each single part, where it is currently located and where it should go. There is also the possibility to manually store or remove parts from stock by using the station located on the side of the sorting system. “This is very useful when cancellations need to be removed or for special parts with special packing that need to be stored, but cannot be conveyed by the designated roller conveyor at the sorting system’s entrance,” explains Damhuis.
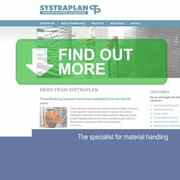
Michels and Damhuis are full of praise for the system and the efficiency introduced shortly after SYSTRAPLAN’s sorting system was installed. „We are operating with a high delivery ratio of an average of 99. 5 % and a throughput time of four days“, says Michels. A condition for this is, however, highest availability of machines and a flawless dispatch. Michels and Danhuis are now less concerned about the latter than in the days of trolleys.