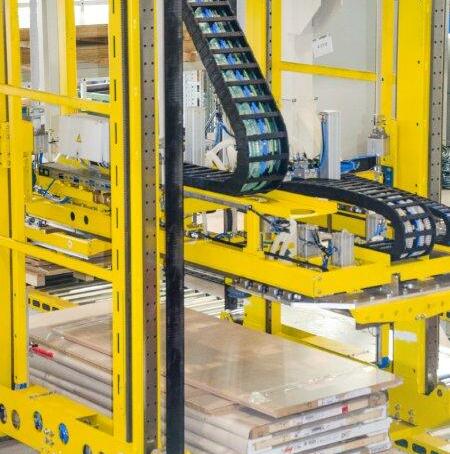
13.October 2016
New Area Storage System with Stack Transportation
The Westag & Getalit AG successfully operates with similar area storage systems based on the same design for many years now. For the customer it was important to fall back on SYSTRAPLAN’s proven technology.
Combined Lift Cage for Stacks
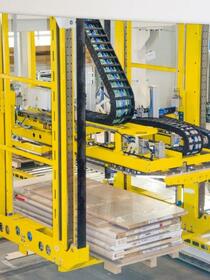
These area storage systems enable to convey stacks and single boards. The space needed in the hoisting system is created by raising the clamp frame by means of a separate lift. For conveying single boards the clamp system is activated by lowering the separate lift.
Safe Stack Transportation – No Board Shifting
For the storage and the retrieval of boards the lift cage is put over the stack. Then transport fingers swivel under the stack and take up the weight of the stack.Underneath the stacks are either pallets or carrier plates positioned on bed lumbers.
Furthermore, the hoisting system is equipped with a suction cup unit for soft fiber strips in order to place these between certain materials. It will be activated on demand.
The systems‘ clamp frame serves to fix the stack by means of its weight whilst conveying the stack, and thus avoids a possible shifting of the doors.
Individual Design Decides Warehouse Performance
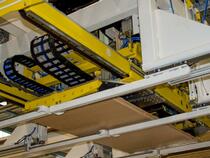
Removal with Direct Connection to Dispatch Department
The retrieval of doors picked is performed on centrally placed conveyors which provide the relevant space to build buffers and to supply the doors directly to the shipping stations. Alternatively, consigned stacks can be build at a central position for subsequent further processing.Waiting Times at Downstream Machines Omit
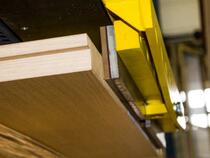
The system places the boards into storage whilst the buffer that was built is being processed by downstream systems.
Fast Access, Automatic Operation
A fast access is guranteed, because the system knows exactly where what is stored and the shortest way for storing and retrieving goods at any time.The system operates whilst the next job is entered or transferred. In the event of waiting times goods can be pre-picked or placed into storage. An appropriate software for these processes was especially created at the customer.
Material is Carefully Handled
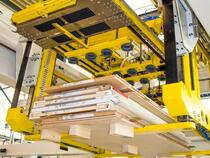
Most suitable for feeding production machines, for intermediate buffers in the production or as exclusive storage system.
Storage and Control System
SYSTRAPLAN’s storage and control program can be operated on standard PC systems under the Microsoft operating system Windows.This guarantees that today’s and tomorrow’s requirements will be met also in future in respect of system design, flexibility and links to standard systems and standard software.