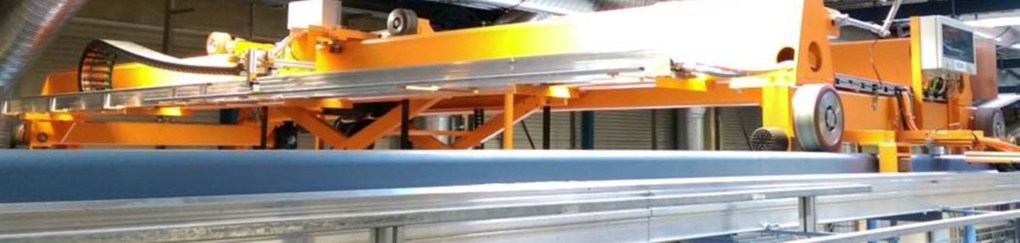
OVERHEAD STORAGE for CASSETTE TRUCKS
[headline=2] The systems are designed for the handling and storage of cassette trucks for the tire industry. The full automatic warehouse for the cassette trucks ensures low personnel costs. Quick access avoids waiting times at the production and a continuous work flow is created.
Floor space is always limited in the production and rather expensive to be used just for storing material. In order to get more floor space in the production the overhead cranes are installed on a platform above the existing production lines.
The floor of the platform includes centering brackets, which are holding the cassettes trucks in a fixed position. The exact design has to be stipulated and is depending on the design of trucks of the customer.
Floor space is always limited in the production and rather expensive to be used just for storing material. In order to get more floor space in the production the overhead cranes are installed on a platform above the existing production lines.
The floor of the platform includes centering brackets, which are holding the cassettes trucks in a fixed position. The exact design has to be stipulated and is depending on the design of trucks of the customer.
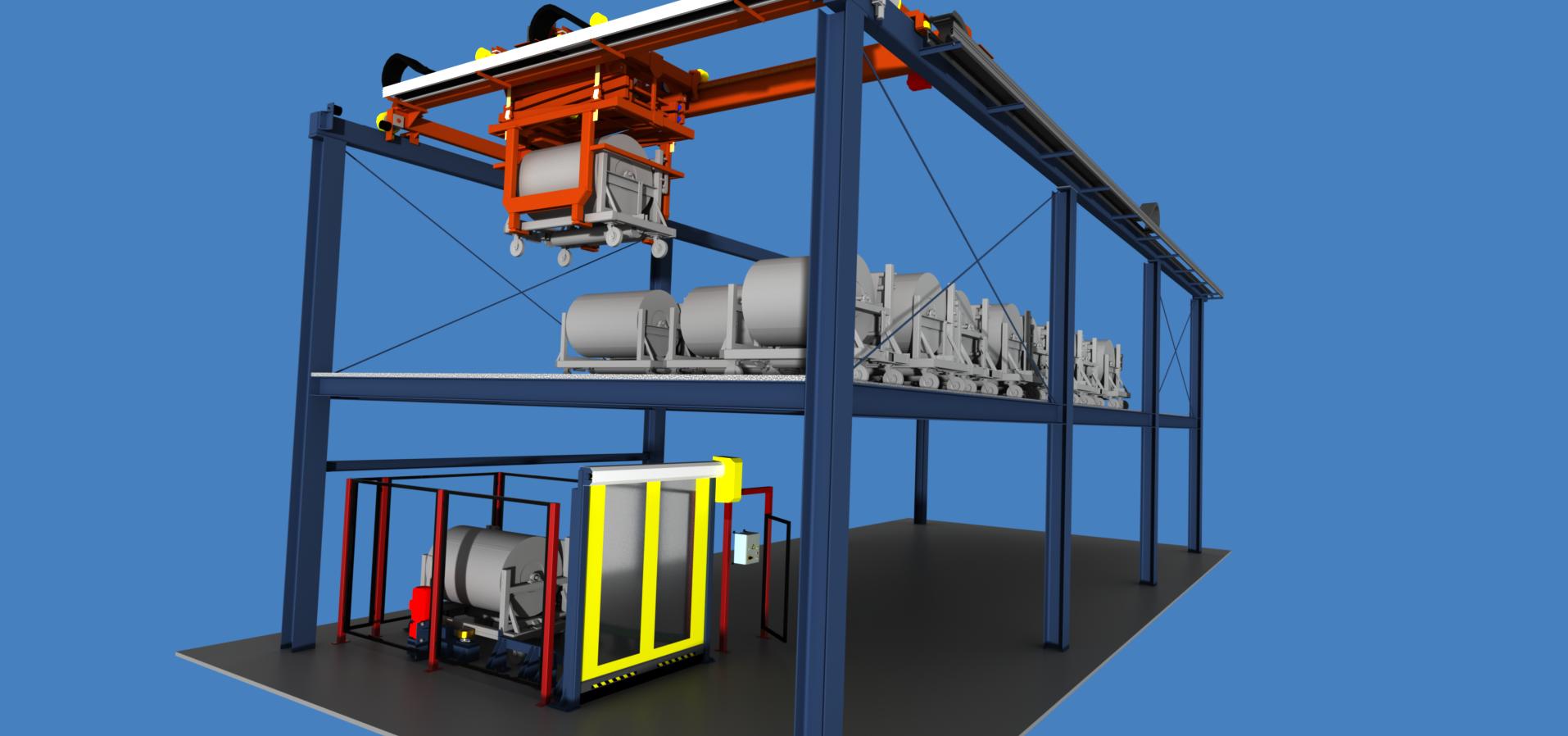
A technical design which makes the difference
Gripping unit with a multiple scissor lifting device
The gripping units for picking up the cassette trucks are placed under the lifting device of the overhead crane. The gripping unite has to be adapted to the customer’s cassette trucks.
A multiple scissor arm lifting device is lifting the cassette trucks from a storage location at the platform or from a charging location at the production floor up to an overhead height. At this overhead height the cassette trucks will be moved across the storage area by the crane.Charging and discharging of the cassette trucks
Each system has several inlets and outlets for the trucks according to the requirements at the production on the floor. The trucks are right there where you need it. The lifting device is reaching through cut-outs of the platform onto the ground level. This charging and discharging places are fenced and equipped with safety light barriers or fast shutter doors. The portal robot will be in a safe position during charging or discharging.
The operator is pulling or pushing the cassette trucks directly out or into the stations. The driven cart transport at the inside of the station is moving the cart automatically into the defined takeover position for the portal robot.
Contour check & drawbar check
The wheels have to be in order and easily turnable. The wheels itself will be checked. The cart is transported by a contour check at the entrance of the station. The contour check is checking the right and left side of the cassettes. The automatic cart transportation is positioning the cart into defined position. At this end position the drawbar is then checked. In this way, largely subsequent collisions with the gripper can be avoided.
After positioning and checking, the lifting device is going down and grips the cart to lift it up to the storage platform. The cart will be taken to an individually selected storage place. This process works also vice versa for discharging as described before.Storage and control program
The data required, i. e. material or quantities needed, must be entered in the control manually. The in-feed stations are equipped with scanners will be installed at each entrance. The control of the system is carried out by a special developed storage program.
SYSTRAPLANs’ storage and control program can be operated under the Microsoft operating system Windows. This guarantees that today’s and tomorrow’s requirements will be met also in future in respect of system design, flexibility and links to standard systems and standard software.
The application has a state of the art graphical screen interface. The user screens are clear, application orientated and easy to use – either by keyboard or by mouse. All information are stored in a standard database.
The personal computer is linked by a special interface with the PLC control system (e.g. Siemens S7). All tasks and handling orders will be executed by this system. Data exchange with a higher ranking production planning and control system is possible via a local area network (LAN). The data transfer can be done e.g. by data base.
Normally, data about the handling jobs and status information about the equipment are transmitted. Such data could be stored, updated and retrieved on a central computer.
The software code is modular and will be adapted for each project to the specific mechanical design of the area storage system and the organization structure of the client.
Horizontal storage systems for the tire industry
We are developing solutions today for your future needs
Let us know your individual requirements.
We will work out a concept tailored to your needs
We will work out a concept tailored to your needs