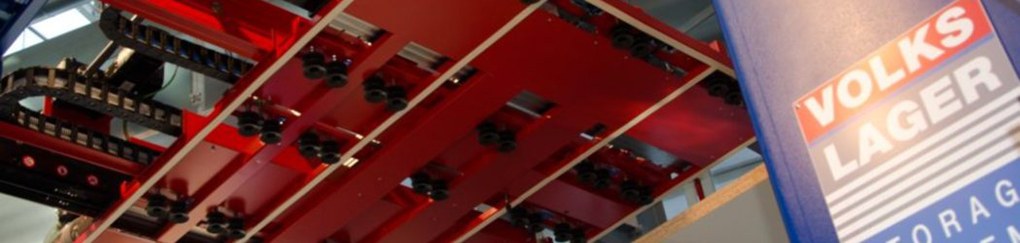
High bay and order picking storage for the timber trade
Order picking of different panel materials and dimensions directly on the rack serve carrier
Short processing times with an ever-increasing range of products and services with growing quantities required an economical solution for panel picking. With a courageous investment in a modern storage and distribution centre for wood-based panels, the service offer for customers and suppliers is improved.An even faster order processing, highest possible availability and especially the highest quality assurance in product handling and delivery are the most important goals that the timber trade is pursuing with such an investment.
It requires a lot of experience to automatically and safely separate the different panel materials and panel dimensions in the high-bay warehouse. But only with this concept the possibility to achieve the required performance is opened up.
Video:
Video-Download
]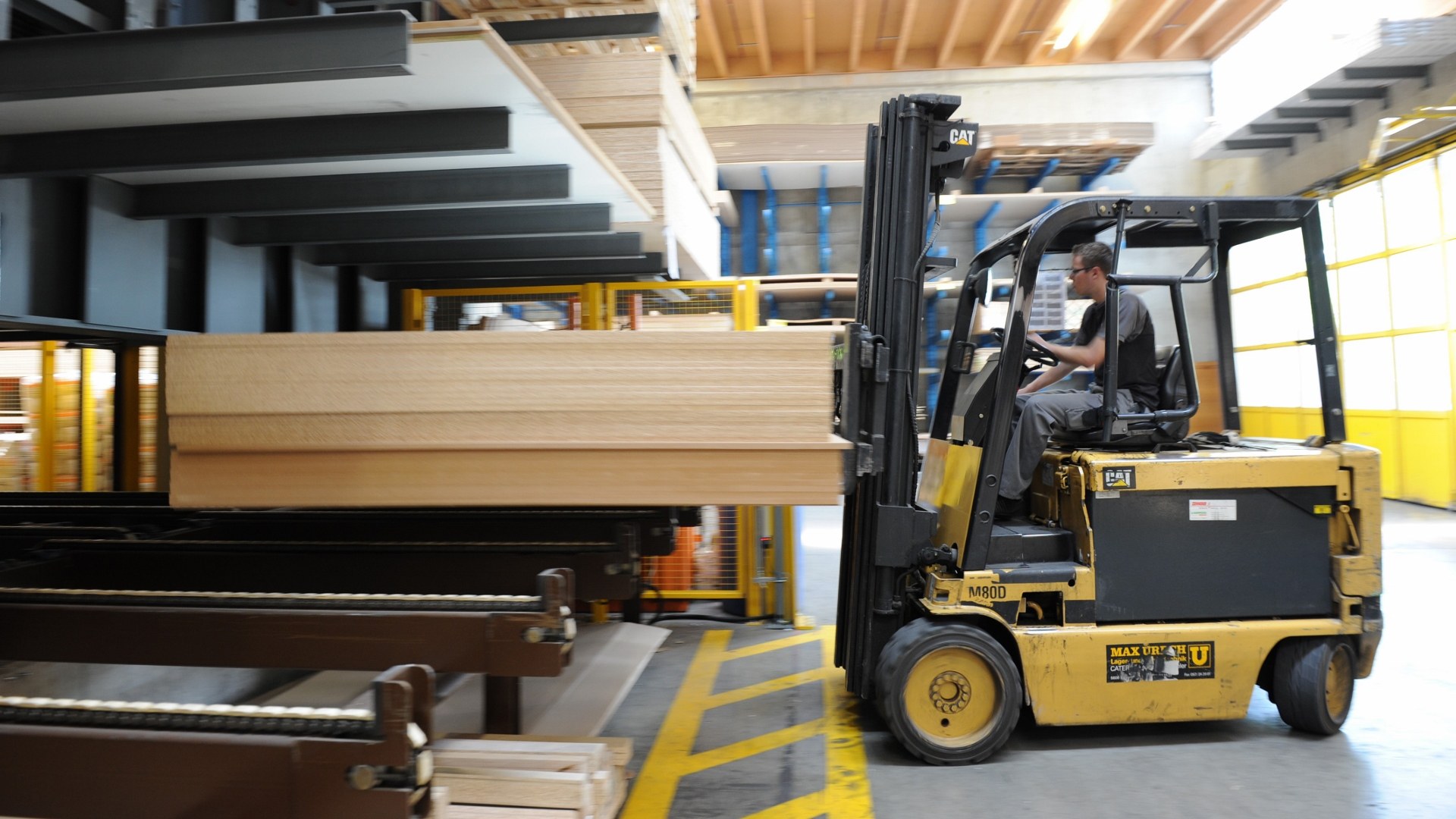
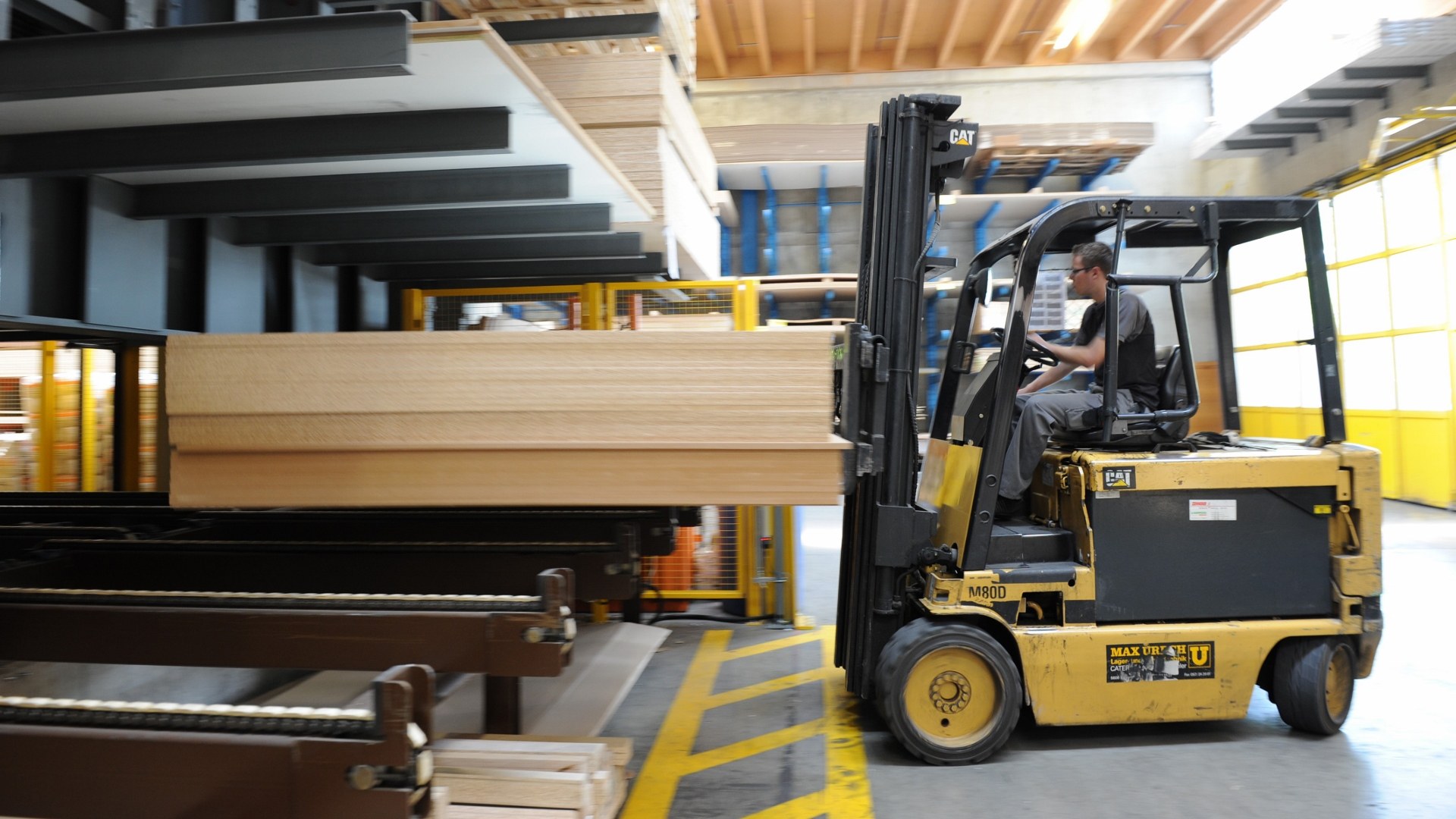
Overview of the essentials
Fast order processing highest possible availability
Direct order picking on the platform of the rack serve carrier
With this high bay storage system, which was developed by Systraplan , stacks as well as single boards are moved.
Among the transport of stacks and single boards the commissioning is directly proceeded in the high bay storage system.
Therefore, an additional area for commissioning is not necessary. Remaining quantities simply stay in stock. This saves time, space, energy and extra appropriation for commissioning.Variable handling of extreme different loads
Whole board-stacks are taken over and are assigned to a storing place by the high bay storage system.
Later the telescopic-suction arms remove single boards from the stack for order commissioning
The load suspension means are prepared and constructed for boards with most different dimensions.
The dimensions vary from 2,800 mm to 5,800 mm in length and 400 mm to 2,500 in width. The high bay storage systems must be able to store stripe materials multiply deep in order to achieve a most possible high filling ratio or complete occupancy. The maximum stack weight can achieve up to 5 tons.Derived timber products are handled damage-free
One of the most important advantages is the damage-free handling of the derived timber products. Within short time the sensitive boards are appropriately prepared for the resale.
By doing so the automatic high bay storage system operates continuously at a comparatively high speed.
It just takes a quarter of an hour to build a consignment of 15 different boards.
Option: Two independently controllable lifting platforms – up to 20% higher output
In comparison to conventional high bay storage systems this system works with two lifting platforms which can be controlled independently. Each platform is equipped with own lifting drives and load suspension devices, which can work to both sides of the aisle.
Due to the independent working from each other up to 20 % higher output in comparison to conventional systems can be achieved.Direct connection to PPS - System
The electronic data processing control ensures fastest feeding and discharging, which facilitates the batch-, package- and piece-wise distribution.
All goods movement data are adjusted just in time by a direct linking of the full automatic high bay storage system with the merchandise management system. Hence, the sales team can always revert to an up-dated asset of boards provided by an easy and interference-proof operating mode.-
Stock-status always available
Systraplans’ storage and control program can be operated under the Microsoft Windows operating system. This guarantees that today’s and tomorrow’s requirements will be met also in future in respect of system design, flexibility and links to standard systems and standard software. -
State of the art graphical screen interface
Referenzen
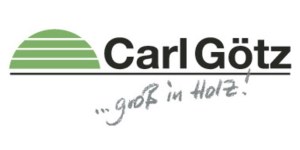
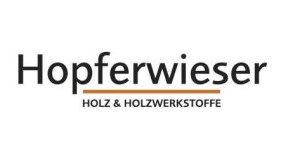
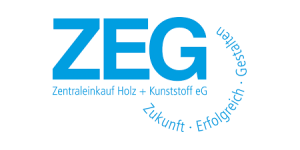
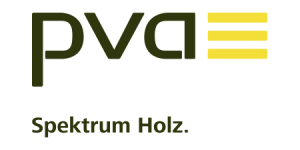
High bay paper storage
We are developing solutions today for your future needs
Let us know your individual requirements.
We will work out a concept tailored to your needs
We will work out a concept tailored to your needs